The P5v2 5-motor walker circuit
An overview of the P5v2 walker
electronics by Wilf Rigter - Feb 2001
This description of operation must be used with the
schematic and layout drawing shown below:
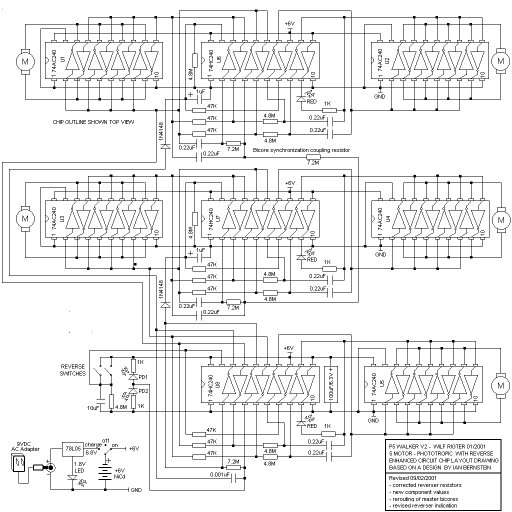
The P5V2 circuit -- click to expand
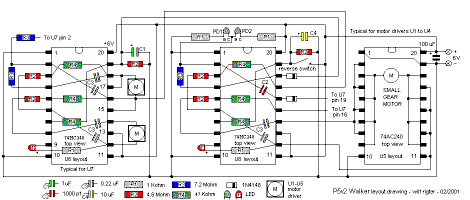
Layout of the P5V2 circuit -- click to
expand
The P5 design uses only eight 74HC/AC240
chips which are all octal inverting buffers. Each 74HC/AC240
chip has two groups of four inverters
each controlled by a tri-state enable pin (pin 1 and
19).
The 74AC240
chips (U1-U5) are used as H-bridge style motor drivers since
they have almost double the drive current compared to
74HC240
chips. These motor driver chips are permanently enabled by
grounding control pins 1 and 19. The two groups each have
four inputs connected in common to a bicore
output and the four outputs are connected in common to one
motor winding terminal. Since each bicore
has two complementary outputs the voltage across the motor
winding causes the motor to rotate back and forth.
The 74HC240
chips U6 and U7 are each used to form a master-slave
bicore
pair with reverser. The inverters
used for the bicores
are permanently enabled by grounding pin 1. The inverters
used for reversing are turned on or off with the tri-state
enable pin 19. Only 2 of the 4 tristate inverters
are used conventionally for reversing the phase of the
slave
bicores
while the other two are put to a novel use: one inverter
is used to provide positive feedback to the enable pin and
the second spare inverter
is used to turn on a RED flashing LED when the reverser is
active. The flashing LED
also provides diagnostic visual indication of the operation
of the slave
bicore.
The 74HC240
chip used for U8 provides a reverser and a slave
bicore
for the waist motor as well as a monocore (a.k.a High Low
Oscillator) photobridge comparator which controls the
phasing of the front and rear motors.
I) The photobridge comparator uses 2 inverters
from U8 connected in series as an voltage controlled
oscillator with complementary outputs to generate three
states :
a. High / low outputs
If the left photodiode
gets more light than the right photodiode,
the two inverter
complementary outputs are steady state DC. The
inverter
with the low output reverses the left slave
bicore
and corresponding rear leg causing the walker to turn
left.
b. Low / high outputs
If the right photodiode
gets more light than the left photodiode,
the two inverter
complementary outputs are steady state DC (opposite to
a.) The inverter
with the low output "reverses" the right slave
bicore
causing the walker to turn right.
c. Both outputs oscillate
If both photodiodes
get equal light, the two inverter
complementary outputs are pulsing and neither of the
slave
bicores
is reversed causing the walker to go straight.
II) Two master
suspended bicores
in U5 and 6 are coupled at their inputs with a 7.2M phase
sync resistor so that they will oscillate in quadrature
with their waveforms overlapping by 25%. These waveforms
are connected to the 74AC240
motor driver which control the front legs.
III) Two rear motor slave
bicores
use inverters
from U5 an U6 with timing components that delay the
slave
bicore
output by about 25%. These are connected to the front leg
motor drivers (6 inverters for each motor).
IV) Two inverters in U6 and U7 are used for signal
reversing and are connected between the outputs of each
of the master
bicores
(front legs) and the slave
bicores
(rear legs) to control turning with enable signals from
the photo comparator circuit. When the light is balanced
pin 19 of U6 and U7 are both high, both reversers are
turned off, the tristate inverters
are disabled and the walker moves straight.
V) The waist slave
bicore
circuit in U8 uses 2 inverters
to control the waist motor driver.
VI) The waist reverser uses two inverters
in U8 and is connected between one output of each of the
U6 and U7 master
bicores
and the waist slave
bicore
circuit inputs described in V). The waist motor phase
reversal occurs when one of two tactile switches is
triggered by collision with an obstacle. At that time the
U8 tristate inverters
are enabled.
VII) The power supply consists of a 6V NiCd battery
and charger circuit with a three position switch for
on-off and charging. A 78L05
is included for recharging a 900mAHr battery pack at 0.1C
without removing it from the walker.
DETAILS OF OPERATION
The Photo Comparator
The photo comparator uses two photodiodes
as a "photo bridge" to sense when the light level on the
left and right photodiodes
is balanced or unbalanced. Two optional resistors are
connected in series with the photodiode
to limit current
in bright light and prevent photodiode
destruction in case of a wrong connection during assembly
and testing. The two photodiodes
must be connected reverse biased in series across the power
supply with the midpoint acting as a voltage divider. It
uses 2 inverters
in U8 connected in series as a High / Low / Oscillate (HLO)
circuit to give complimentary steady state outputs when the
photodiodes
are unbalanced.
Both inverter
outputs will oscillate when the light on the photodiodes
is balanced and the photo bridge midpoint voltage is near
the switching threshold of the first inverter
input. A small capacitor
(0.001uf) connected from the output of the second inverter
back to the midpoint of the photodiode
bridge provides positive feedback for oscillation and
reduces frequency and power consumption. The ouputs of the
HLO are connected through diodes
to discharge capacitors
on the tristate enable (pin 19) of the reverser circuits in
U6 and U7. The capacitors
remain discharged as long as the \HLO output is pulsing or
steady state high. The value of the capacitor
/ resistor
on U6/7 pin 19 scan be adjusted if required to give a faster
or slower response to differential light change.
When the photo bridge is unbalanced, the midpoint voltage
of the bridge stops the HLO oscillation. One HLO output then
goes low steady state and a capacitor
at the corresponding reverser tristate input (pin 19)
discharges through the parallel resistor
until the threshold is reached enabling the turning
reverser. Note that one of the controlled inverter's
outputs is connected through a resistor
to pin 19 for positive feedback to quickly discharge the
capacitor
when crossing the threshold to provide a snap action in the
reverser operation. A second inverter
is used to connect a red LED
to one slave
bicore
ouput.
The Master Bicores
The master
bicores
generate the two sets of central pattern signals which are
phase locked in quadrature with synchronization coupling
resistor. Interestingly, this method of phase locking relies
on the fact that normally both bicore
are oscillating at nearly the same frequency but with one
slightly faster than the other. This faster bicore
will "pull" the frequency of the slower bicore
and effectively "enslave" that master
bicore.
However with perfectly matched components and the two could
switch roles and while frequency locked, they would wander
back and forth in phase relationship!
The Reversers
The reversers are sometimes called Mat Muxes and their
function is to control the phase inversion of pairs of
signals. This is done by routing the signals through one of
two parallel paths:
a) inverted signal through a tristate inverter
or
b) non-inverted signal through a resistor
when the tristate inverter
is disabled.
For U6 and U7 the complementary outputs from the
master
bicore
connects to the reverser which when enabled by photodiode
comparator is used to add 180 degree phase shift to the
signal from the master
to the slave
bicore
and subsequently, shifts the front and rear legs rotations
phasing by 180 degrees. Note that the waist reverser in U8
uses one output each from the two master
bicores
and when enabled by collision switches, changes the phase
angle of the waist rotation.
The Slave Bicores
The slave
bicores
delay the phase angle of the front legs with respect to the
rear legs which are controlled by the master
bicores.
The reversers between the master
and slave
bicores
determine whether the front and rear legs (on opposite
corners) are moving in the same or opposite direction when
the legs are on the ground. This causes the legs to both
move forwards or backwards together or to rotate the body of
the walker slightly with each step of those legs until the
light level is balanced on the two photodiodes.
The operation of the reversers and the slave
bicore
is indicated with flashing red LED
when the reverser inverters
are enabled.
The Motors and Legs
Five motors are used to control rotation of each of the
four legs and the waist. The leg motors are mounted nearly
vertically with an L-shaped reciprocating legs swinging in
an arc front to rear. Only two legs are pushing against the
floor at one time. The reciprocating waist motor is mounted
horizontally raising one pair of legs in the air while the
other pair of legs are lowered on the floor. Depending on
the phase angle of the waist motor, the legs are lowered on
the floor on the front or the rear stroke of the legs and
therefore determines the forward and reverse direction. When
a turning reverser is active, one set of diagonal legs moves
forward or backwards while the other set rotates the walker
clockwise or counter-clockwise around it's center. The net
effect of this is a sweeping turn motion.
The 74AC240
motor driver chips (U1-U5) can be used to control small
efficient gear motors such as converted hobby servos or
camcorder / LCD projector lens motors. Gear ratios of 40-100
provide the right combination of torque
and RPM. The maximum current
at 6V should be less than 150ma to avoid overheating the
motor driver chips. If desired the 74AC240s
can be replaced with five higher current
H-bridges or five DPDT relays.
The Power Supply
The last part is the power supply which consists of a 6V
NiCd battery pack and a charger circuit designed to be used
with a wall type AC adapter. A switch is included to turn
the walker on or off or to connect the battery to the
charger circuit. The 78L05
provides constant current
charging until the maximum float voltage is reached. A red
LED
in in series with the 5V regulator ground
reference raises the output voltage to the 6.8V float
voltage required for a 6V NiCd battery and also indicates
when the AC adapter power is ON. The 78L05
limits the current
to 100ma with thermal shutdown in case of an overload to
ground.
This current
is meant to charge a battery
at a safe 0.1C rate and therefore must be used with a 6V
NiCd battery
with at least 900mAhr capacity. Red LEDs
have varying (1.6V-2.0V) forward voltage drops and the red
LED
for this application should be efficient and selected for a
1.8V drop to set the charge open circuit output voltage to
6.8V.
For more information...
|
Wilf has posted assembly and test instructions for
this circuit here.
|
|