BEAM Techniques is a BEAM
Reference Library
site.
|
|
Transferring your design to a
board
Getting from diagram to
traces
There are six methods (that I'm aware of) to turn your
circuit design into an echant resist pattern on a
copper-plated board:
Lets look at these, one at a time (later I compare them all
side-by-side)...
Resist pattern applied via ink pen
and / or transfer material
Here, you transfer your design to the board by
using a permanent marker (most any "permanent" black
marker will do) or rub-on transfer sheet to mark out
where you want copper traces. The pen's ink resists the
etchant, thus creating the desired circuit on the board.
While cheap and simple, note that it is difficult to
position the traces accurately (this can be a real
problem if you are using ICs in your design). Also, since
pens don't necessarily apply ink uniformly, there is a
risk that some traces will be etched away since etchant
can get to the copper through a thin layer of resist.
I've read all sorts of articles about some project or
another using this method of board building, so
apparently it works for somebody. As for myself, this
method has been the cause of no end of frustration -- the
transfer sheet traces always wind up sticking better to
my fingers than to the board, and the pen traces never
seem to hold up to the etchant. Maybe I'm just a complete
klutz, but I really can't recommend these methods.
Resist pattern applied via
a laser printer and "Press-N-Peel" sheets 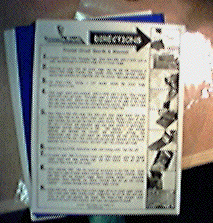
If you have access to a copier or laser printer,
this is a handy way to get very sharp traces, using
"Press-N-Peel" sheets from Techniks.
Direct from Techniks,
the sheets cost about $1.50 each ($US, in quantity), you
can also get packets with fewer sheets (but of course, at
a higher per-sheet cost) from many electronic supply
stores. Here are the steps:
- Photocopy or laser print your design onto the
non-glossy (emulsion) side of the "Press-N-Peel"
material. Since this stuff isn't terribly cheap, rather
than printing onto whole sheets, I just trim off a piece
of PNP of the appropriate size, tape it to a blank sheet
of paper, and print on to that.
- Place the PNP (with printed design, emulsion side
down) on to your prepared board, and iron with a
300° (F) clothes iron.
- After a few minutes, the board, PNP, and iron are all
at the same temperature -- quench the board and PNP under
cold water, and peel the PNP film off. You'll now have a
shiny copper board with even shinier dark blue traces
where you want your copper to end up.
- Proof your board (fill in any missing pieces of
traces with transfer material or resist pen, pull off any
"fills" between traces with packing tape), and you're
ready to etch.
This stuff has worked just fine for me, as long as I'm
patient, and clean my board sufficiently. It also helps
to iron on a firm surface (i.e., scrap of plywood) rather
than on something soft like an ironing board. I also put
a sheet of paper between the PNP and the iron, just to
reduce the chance that friction will cause the PNP film
to slip around. I've never had problems with bad traces
-- just scattered "bubbles" in the middle of large
"black" regions (due to a speck of dust inadvertently
stuck to the PNP film). I just touch up these spots
before etching -- "super glue" works, as does nail
polish.
Resist pattern applied
via a laser printer and "Toner Transfer Paper" or
"Press-N-Peel Wet"
This method is much like the "Press-N-Peel"
method above, but uses "Toner Transfer Paper" from
DynaArt
Designs (or if you can find it, "Press-N-Peel Wet"
sheets from Techniks).
Here, you iron the paper on to the board, then soak them
together until the water soaks through the paper and
dissolves a coating that held the toner to it. The toner
provides the etch resist. This method works very well,
although large areas of protected copper tend to wind up
looking "mottled" as the toner doesn't provide 100%
protection. For what it's worth, this paper costs about
twice as much as regular "Press-N-Peel"
sheets.
Resist pattern applied via a
laser printer and clay-coated (i.e., magazine) paper
This method is much like the "Press-N-Peel"
method above, but uses plain clay-coated paper instead of
a proprietary film. Essentially, you iron the paper on to
the board, then soak them together in soapy water until
the paper basically falls apart (leaving a coating of
clay stuck to the board to act as resist). Here's a
promising
description; another, more detailed one is here.
This method seems to live or die based on the paper you
use (it needs to be clay coated, but not so thick that
the iron won't heat the toner thoroughly). I've been told
that Epson's Photoquality Inkjet paper #S041062 works
well...
Resist pattern applied via
"blender pen"
This method comes courtesy of Jesse
Willis:
What I did was swing by my local art store
and pick up an Eberhard Faber Design Art Marker, Broad
Nib 311 Colorless Blender (only about $2 US). With
this, you simply photocopy the circuit you wish, and
then lay the photocopy face down on the PCB. Run the
marker over the back of the photocopy, and the
image transfers to the copper.
Resist pattern applied
via photolithography
In this case, a board is covered with a resist
material that sets up when exposed to UV light. To make a
board this way, you start by making a photo negative of
the circuit which is clear where you want a circuit
trace, and opaque where you don't want a trace. After the
photo negative is made from your art work, it is placed
onto the photo sensitized board, and is exposed to the
UV. The UV light transmits through the clear portions of
the negative and cures the photo resist. After that, the
board is submerged into a developer bath that develops
the traces on the board. The resist that is left is in
the shape of the art work that represents your circuit.
This approach is accurate and makes neat traces, and
the photo negative can be used over and over to make
additional boards. However, you need your own photo lab
to do the board developing, and the entire process takes
quite a bit of time.
There's a good tutorial here
on photolithography (the tutorial's useful even if you
don't want to use this method).
Comparison
Resist Mask
Creation Method
|
Price
|
Process Complexity
|
Results
|
Ink pen /
transfer material
|
Very low
|
Simple, but time-consuming.
|
Functional, if not (in general) particularly
aesthetic. Difficult to get accurate hole alignment
for ICs, sometimes difficult to get traces that
reliably survive etching.
|
"Press-N-Peel" sheets
|
Medium recurring cost ($1.50 US per sheet of PNP
film)
|
Medium complexity, but few manual steps; manual
"touchup" of resist areas often required
|
Good, but you must be obsessive about cleaning
your board (and keeping your PNP film clean), and
vigilant about checking / "touching up" traces
before etching the board
|
"Toner Transfer Paper"
|
Medium recurring cost ($3.00 US per sheet of
paper; in bulk, cost can be as low as $2.00 per
sheet)
|
Medium complexity, but few manual steps
|
I have yet to test this method yet.
|
Clay-coated paper
|
Low (a few cents per page of paper, plus
etchant)
|
Medium complexity, but few manual steps; manual
"touchup" of traces sometimes required
|
A bit less detailed than "Press-N-Peel" (based
solely on description, I have yet to find paper
that works)
|
Blender pen
|
Low (a few dollars for the blender pen, plus
etchant)
|
Medium complexity, but few manual steps; manual
"touchup" of traces sometimes required
|
I've heard good things, but have yet to test
this yet myself.
|
Photolithography
|
High setup cost (darkroom, light box, initial
stock of developing chemicals), medium recurring
cost (photosensitized boards, replacement
chemicals)
|
High; light box, developing chemicals, darkroom
usage required
|
Very good
|
Store-bought
|
High, unless you want many copies of a single
board design
|
Low (for you) -- send off board design &
credit card number in email, receive boards at your
doorstep. No muss, no fuss, no drilling dozens of
tiny little holes...
|
Professional quality boards; cost-effective for
multiple boards (i.e., not "onesy-twosy"
productions).
|
For more information...
|
The RobotRoom
has its own take on building PCBs here.
Bruce Robinson posted some handy tips on PCB
building to the BEAM list here.
I've got a page on drill bit sizes (for use in
PCB building) here.
|
|