A
ball caster is a type of 'wheel' that allows smooth
movement in all directions. A miniature ball caster
would be a wonderful addition to a light-seeking
BEAM robot, reducing the friction from a
tail-dragging capacitor. And it provides an
alternative to a tail wheel for other wheeled bots.
Most commercial versions, which come with balls
from 1" and up, are too large and heavy for
miniature robotics. Smaller casters are available
but are expensive.
This article describes a low-cost, light-weight
alternative in the BEAM tradition of scavenged and
recycled parts.
Parts list
|
Cross-section
|
- Telescoping Antenna
- Ball bearing to fit
- Spring from ball point pen
- Small nut and bolt for
mounting
- Plastic or nylon cylinder
(optional)
- Tubing cutter (optional)
|
|
A telescoping antenna from any broken radio or
minisystem is a low-cost alternative to expensive
telescoping brass tubing from a hobby shop.
Disassemble the antenna by cutting off the ball or
cylindrical tip and any badly damaged metal from
the bottom end. Push each section through from the
top using a piece of stiff wire (caution: there are
little brass bits inside that will fly around as
they pop out!). This will give you several pieces
of nicely chromed telescoping tubing. Note that one
end of each section is swaged, that is, it has a
slightly curved 'shoulder'.
The next trick is to find a ball bearing
(shortened from here on to BB, but don't try to use
Daisy BBs intended for an air rifle, as they aren't
round enough!) that fits into one sleeve of the
tubing. I asked a local bike shop to save old BBs
for a week, and got a wonderful if greasy
selection; but you can buy them in little
containers at many hardware or sports stores. The
BB should drop into the tube easily but be caught
by the swaged (curved) shoulder at the end.
BTW, if you are making several casters of the
same diameter, you can use a tubing cutter. This
little tool will not only cut your tubing to
length, it will also swage it at the same time. Use
the tubing cutter to make your tubes twice as long
as you need them (and maybe a little more) then saw
them in half. This will give you tubes with one
swaged end and one straight end.
|
|
Tubing cutter
|
Diagram of cuts
|
In the version shown, I used the tip from an old
mechanical pencil as a 'friction bearing' or
'pusher' to hold down the BB and minimize friction.
But I have also used bits of nylon tubing, plastic
washers, and nothing, all with reasonable success.
I was just intrigued by the shape of the pencil tip
and thought it would fit in beautifully, which it
did.
I cut off the tip, and drilled out the center a
bit with a 3/8" drill to make a little 'cup' that
the BB would fit in. But if you skip this part
entirely, your ball caster should still work.
Next you need a spring. Pick one from your junk
box that will fit inside the antenna tubing and
push the ball against the shoulder. For the caster
shown here, I used part of a ball point pen spring.
If you are not using a 'friction bearing,' check
the spring for sharp ends and file smooth if
necessary (at least the end that goes against the
ball). Here is where a good set of needle files
comes in handy! Another BTW, I have made ball
casters without the springs, provided I had some
kind of nylon bushing to hold the ball in place.
But it seems to be easier to find a spring the
right size than to find a nylon bushing the right
size....
Now, decide how long you want your caster to be.
If you have a bot in mind, measure the distance
from workbench to chassis. Use a hacksaw, hobby
saw, or dremel cut-off wheel (safety glasses,
please for this last) to cut the tubing the right
length.
The spring should be slightly compressed between
the ball and the mounting nut, but if it is too
squished, the ball won't turn. Use your cut-off
wheel or file to cut the spring shorter if
necessary. When the spring tension is right, you
should be able to push the ball in with your
finger, but the weight of the bot will not move the
ball much at all. The figure below shows all the
parts so far, laid out in order.
Last step! Find a little nut and bolt for
mounting. The nut should just fit into the end of
the tube. If the nut's a little small, you can
GENTLY squeeze the tubing a bit so the nut will
wedge in. If the nut's a bit too big, you may have
a bit of work ahead with the Armstrong milling
machine (that's a file). Once you have the nut in,
hold it with your finger (to avoid that sproing!)
and check the tension again. If all is well,
disassemble, clean everything carefully (including
the inside of the tube-a pipe cleaner works okay
here) to bet rid of any filings or dirt, and
reassemble with a little Vaseline or bearing grease
(or, if you prefer, assemble dry and later spray in
a little WD40 or whatever). Clean off the open end
of the tube and solder the mounting nut into
place.
The figures below show the caster mounted on a
robot chassis made from the front of an old
stereo.
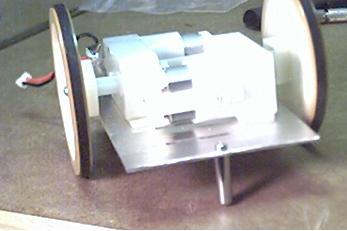
I have tried other mounting methods. My first
try involved slotting the tubing and folding little
flaps in to hold the spring then epoxying the whole
assembly to the chassis. This worked tolerably
well. Another version had flaps folded out to
increase the gluing surface. The method shown here,
while a bit more work, gave the best-looking result
and is the method that lets me easily relocate or
reuse a caster.
|