At a simplistic level, using DC
motors is pretty straightforward -- you put power
in, and get rotary motion out. Life, of course, is
never this simple -- there are a number of
subtleties of DC
motor behavior that should be accounted for in
BEAMbot
design.
High-speed output
This is the simplest trait to understand and
treat -- most DC
motors run at very high output speeds (generally
thousands or tens of thousands of RPM).
While this is fine for some BEAMbots
(say, photopoppers
or solarrollers),
many BEAMbots
(walkers, heads) require lower speeds -- you must
put gears on your DC
motor's output for these applications.
Back EMF
Just as putting voltage across a wire in a
magnetic field can generate motion, moving a wire
through a magnetic field can generate voltage. This
means that as a DC
motor's rotor spins, it generates voltage -- the
output voltage is known as back EMF.
Because of back EMF,
a spark is created at the commutator as a motor's
brushes switch from contact to contact. Meanwhile,
back EMF
can damage sensitive circuits when a motor is
stopped suddenly.
Noise (ripple) on power lines
A number of things will cause a DC
motor to put noise on its power lines: commutation
noise (a function of brush / commutator design
& construction), roughness in bearings (via
back EMF),
and gearing roughness (via back EMF,
if the motor is part of a gearmotor) are three big
contributors.
Even without these avoidable factors, any
electric motor will put noise on its power lines by
virtue of the fact that its current
draw is not constant throughout its motion. Going
back to our example two-pole motor, its current
draw will be a function of the angle between its
rotor coil and field magnets:
Since most small DC
motors have 3 coils, the coils' current
curves will overlay each other:
Added together, this ideal motor's current
will then look something like this:
Reality is a bit more complex than this, as even
a high-quality motor will display a current
transient at each commutation transition. Since
each coil has inductance
(by definition) and some capacitance,
there will be a surge of current
as the commutator's brushes first touch a coil's
contact, and another as the brushes leave the
contact (here, there's a slight spark as the coil's
magnetic field collapses).
As a good example, consider an oscilloscope
trace of the current
through a Mabuchi FF-030PN motor supplied with 2 V
(1ms per horizontal division, 0.05 mA per vertical
division):
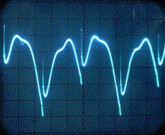
In this case, the peak-to-peak current
ripple is approximately 0.29 mA, while the average
motor current
is just under 31 mA. So under these conditions, the
motor puts about less than 1% of current
ripple onto its power lines (and as you can see
from the "clean" traces, it outputs essentially no
high-frequency current noise). Note that since this
is a 3-pole motor, and each coil is energized in
both directions over the course of a rotor
rotation, one revolution of the rotor will
correspond to six of the above curves (here, 6 x
2.4 ms = 0.0144 sec, corresponding to a motor
rotation rate of just under 4200 RPM).
Motor power ripple can wreak havoc in Nv nets by
destabilizing them inadvertently. Fortunately, this
can be mitigated by putting a small capacitor
across the motor's power lines (you'll only be able
to filter out "spikey" transients this way, though
-- you'll always see curves like the ones above
being imposed on your power). On the flip side of
this coin, motor power ripple can be put to good
use -- as was shown above, ripple frequency can be
used to measure motor speed, and its destabilizing
tendencies can be used to reverse
a motor without the need for discrete "back-up"
sensors.
To scope out what motor is best for a given BEAM
application, we'll need to do some math -- let's
move on to DC
motor performance
parameters.
|